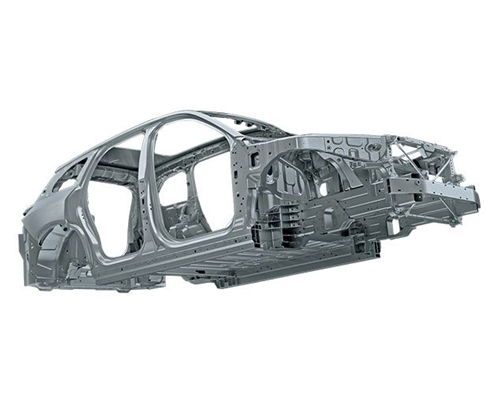
- Project Overview
- Project proposals
- Project Craft
- Project equipment list
- Project site photos
Laser welding of Weilai ES8 all-aluminum body
As a new force for new energy vehicle manufacturing, Wei Lai officially released its first full-size pure electric SUV ES8 on December 16, 2017. The 96.4% aluminum usage rate makes the car an all-aluminum body aluminum in the global production car. The model with the highest material content, excellent structural design and advanced connection technology make the torsional stiffness of the whole vehicle up to 44,140 Nm/degree.
Tong Hi-Tech is responsible for the development and testing of the laser welding process of the entire vehicle, as well as the manufacture of the laser welding part of the ES8 prototype trial production.
圖1-蔚來ES8產(chǎn)品宣傳圖
圖2-蔚來ES8全鋁合金白車身
The ES8 body-in-white design uses 7 different aluminum alloy connection technologies:
? Laser welding (Laser)
? Hot melt self-tapping riveting (FDS)
? High-strength core pulling (Monobolt)
? Self-piercing riveting (SPR)
? Aluminum spot welding (RSW)
? Cold metal transition arc welding (CMT)
? Adhesive
圖3- ES8白車身7種鋁合金連接技術(shù)
Tong Hi-Tech has developed, tested and prototyped the laser welding process for Weilai's ES8 all-aluminum body. The laser welding process design includes wire-filled fusion welding and one-dimensional scanning deep fusion welding.
The laser welding seam of the whole vehicle is up to 64 meters. The laser welding process includes wire welding and one-dimensional scanning deep welding. The welding area involves the four door frame area, the side wall ABC column area, the roof area, and the front cabin crossbeam area. Etc., which provide strong support for the lightweight of the whole vehicle.
Laser one-dimensional deep penetration welding has become the mainstream application process for aluminum alloy welding. It can not only solve the difficulties caused by "small holes" in aluminum alloy welding, but also effectively avoid the occurrence of welding cracks and ensure the stability of welding quality. Common processing tools on the market are represented by the LSK05 system laser head of ThyssenKrupp in Germany:
![]() | 激光頭LSK05-08的優(yōu)勢 ? 加工速度快 ? 能耗低,組件變形減少 ? 出色的強度/剛性 ? 高電位自動化,所需空間小 ? 易損件需求低 ? 法蘭寬度減小/重量輕 ? 獨立于焊件厚度 ? 可變焊縫 ? 延遲減少 ? 有效焊縫長度增加 ? 鋁合金焊接能力提高 |
一維振動 |
ü The accompanying fixture can effectively ensure the welding gap between the plates, and can solve the welding quality defects caused by the matching of the workpiece to the maximum extent;
ü With 800HZ high frequency scanning technology, it can effectively provide the stability of aluminum alloy welding quality;
ü The unique double-finger structure design makes the welding flange edge narrow to 4-6mm, which is beneficial to the lightweight design of the car body
圖4- ES8焊接試片金相照片
圖7-南京蔚來現(xiàn)場焊接圖
Based on the light weight of the vehicle, from the perspective of manufacturing, the welding of all-aluminum body of ES8 is undoubtedly a huge challenge. Not only the production line and raw material input costs increase, but also a strict production process.
The pre-development, testing and prototype production of the same high-tech is to find problems and solve problems through small batch production. The R&D team of Tonggao will dissect each body part one by one, research the end face and connection points after cutting, and adjust the equipment parameters according to the problem, such as robot welding posture, pressing force, laser power, scanning frequency, etc., to ensure that Meet the customer's high-volume production requirements.
The same high-tech quality management system is set and implemented according to the highest industry standards, which strongly guarantees the landing quality of ES8 body in white and ensures the delivery of excellent quality ES8 to customers.
Tonggao Advanced Manufacturing Technology (Taicang) Co., Ltd.
Author: Gu Luo Yan
Technical support: Feng Zhi
Sales consulting: Jin Ailong
May 7, 2018